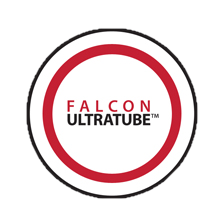
Ultratube™
Seamless Engineering Thermoplastic Liner
Falcon Ultratube™ is a liner manufactured from a proprietary blended PolyPhenylene Sulfide thermoplastic resin specially formulated for use in downhole oil and gas production environments. This third generation of Falcon liners is similar to the other liners in dimensions and mechanical bonding. Ultratube has a significant increase in temperature stability, tensile strength, abrasion and chemical resistance over the other proven Polycore Liners. The innovative polymers in this liner offer the broadest range of resistance to solvents, steam, strong bases, fuel, and acids. The new polymers are specifically designed to limit the permeability of acid gases such as CO2 and H2S.
Some uses or applications of this product may be covered by one or more patents.
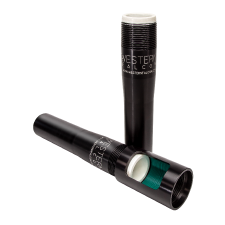
Coated couplings to protect J-area against corrosion
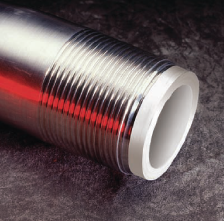
Liner face provides pin thread protection.
Falcon Ultratube™ is a liner manufactured from a proprietary blended PolyPhenylene Sulfide thermoplastic resin specially formulated for use in downhole oil and gas production environments. This third generation of Falcon liners is similar to the other liners in dimensions and mechanical bonding. Ultratube has a significant increase in temperature stability, tensile strength, abrasion and chemical resistance over the other proven Polycore Liners. The innovative polymers in this liner offer the broadest range of resistance to solvents, steam, strong bases, fuel, and acids. The new polymers are specifically designed to limit the permeability of acid gases such as CO2 and H2S.
Some uses or applications of this product may be covered by one or more patents.
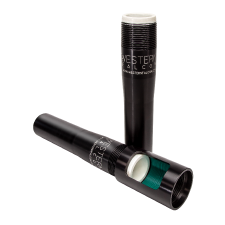
Coated couplings to protect J-area against corrosion
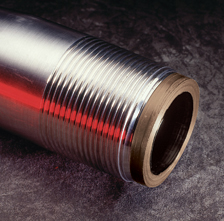
Liner face provides pin thread protection.
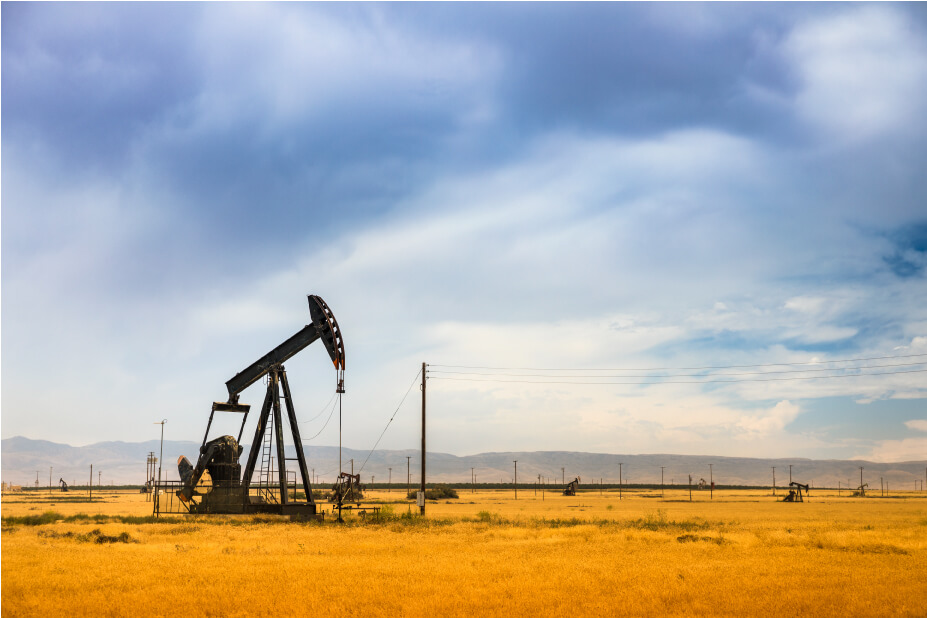
Beam Pumped Wells
PC Pumped Wells
Submersible Pumped Wells
Gas Lift Wells
Coal Bed Methane
Acid Gas Injection
Disposal
Flow Lines
Solution Mining
Corrosion control
Reduce well servicing frequency and cost
Reduce tubing and rod failures
Reduce corrosion inhibitor requirements
Eliminate rod guides
No stabbing guides or special connection inserts
No need for field service technician
- Maximum operating temperature is 176° C (350° F)
- Coated couplings to protect J-area against corrosion
- Minimum API torque recommended for tubing connection make-up
- No special position make-up required
- Steam Flood
- Beam Pumped Wells
- PC Pumped Wells
- Submersible Pumped Wells
- Plunger Lift Wells
- Gas Lift Wells
- Coal Bed Methane
- Acid Gas Injection
- Water Injection
- Disposal
- Flow Lines
- Solution Mining
- Mitigates rod on tubing wear
- Corrosion control
- Reduce well servicing frequency and cost
- Reduce tubing and rod failures
- Reduce corrosion inhibitor requirements
- Reduce friction and peak polish rod load
- Eliminate rod guides
- No stabbing guides or special connection inserts
- No need for field service technician
- Maximum operating temperature is 176° C (350° F)
- Coated couplings to protect J-area against corrosion
- Minimum API torque recommended for tubing connection make-up
- No special position make-up required
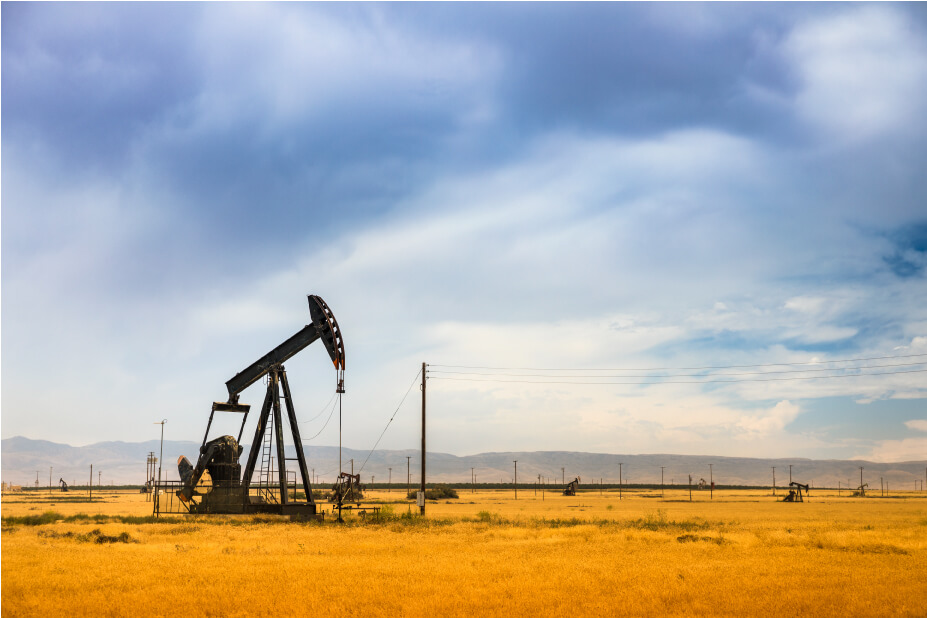
Contact your Field Representative Today for a Customized Solution
Polycore, a subsidiary of Western Falcon Energy Services, has demonstrated success in over 20 million meters (70 million feet) of pipe in the last 20 years! There is not a well we can’t fix.